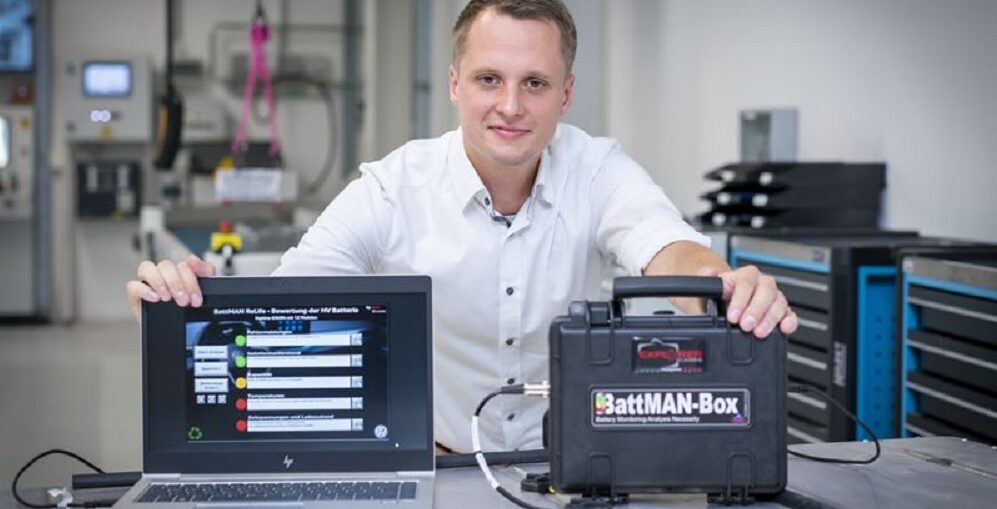
Audi on kehittänyt sähköautojen akustojen pikatarkastusjärjestelmää, jonka avulla niiden kunto selviää muutamassa minuutissa. Aiemmin prosessi on kestänyt useita tunteja. Testerin ensimmäinen versio on Audin lisäksi muidenkin Volkswagen-konsernin automerkkien käytössä.
Audi kehitti BattMAN (Battery Monitoring Analysis Necessity) -ohjelmiston alkuaan uuden e-tronin korkeajänniteakun analysointia varten. Testillä haluttiin selvittää, mitä kennoja ja moduuleja voidaan uusiokäyttää, joko uudelleen joko kokonaan tai osittain esimerkiksi energiavarastona tai uusien akkujen materiaalina.
Testillä määritetään akun yleiskunto, ja tämän jälkeen on kolme vaihtoehtoa: Ensimmäinen vaihtoehto on ns. uudelleenvalmistus, jossa akku voidaan sen hyvän tai erittäin hyvän kunnon vuoksi käyttää tarvittavien korjausten jälkeen sähköajoneuvon varaosana. Varaosakäyttöön liittyviä konsepteja valmistellaan yhtiössä parhaillaan.
Pienjänniteliitäntöjen kytkemisen jälkeen laite tarkistaa ensin, pystyykö akku kommunikoimaan ja siirtämään dataa. Tämän jälkeen järjestelmä tutkii ja osoittaa mahdolliset virheilmoitukset sekä eristysresistanssin, kapasiteetin, lämpötilat ja kennojännitteet.
”Pystymme mittaamaan kennon kaikki tärkeimmät parametrit. Liikennevalojärjestelmä kertoo jokaisen kennon tilan: vihreä kertoo, että kenno on hyvässä kunnossa, keltainen kertoo tarkemman tarkastuksen tarpeesta ja punainen kertoo, että kenno on epäkunnossa”, selvittää Audin laatuinsinööri Axel Vanden Branden.
Toisessa vaihtoehdossa keskimääräisessä tai hyvässä kunnossa oleva akku saa uuden elämän, jolloin sitä käytetään vielä vuosia muualla kuin sähköautossa. Uusi käyttöpaikka voi olla joustava pikalatausasema, latausrobotti, autonominen kuljetusjärjestelmä, trukki tai kotitalouden energiavarasto tai varavirtajärjestelmä.
Kolmas vaihtoehto on materiaalien kierrätys Audin Salzgitterin pilottitehtaalla, jossa akut puretaan raaka-aineiksi, kuten alumiiniksi, kupariksi, muoviksi ja jauheeksi, joka sisältää arvokkaita akkukomponentteja, kuten litiumia, nikkeliä, mangaania, kobolttia ja grafiittia. Yrityksen yhteistyökumppanit erottelevat akkukomponentit hydrometallurgisesti ennen kuin ne prosessoidaan uudelleen katodimateriaaliksi.
Konsernille uusi akkujen kehityskeskus
Volkswagen-konserni panostaa suurien autonvalmistajien tapaan sähköautojen lisäksi niiden tekniiikan kehittämiseen. Konserni investoi 70 miljoonaa euroa akkututkimuksen laajentamiseen ja luo noin 250 huipputeknologian työpaikkaa.
Yksi merkki siitä on Saksan Saltzgitterissä avattu akkukennojen laboratoriokeskus. Tulevaisuudessa noin 250 asiantuntijaa neljässä laboratoriossa tutkimusta kennojen kehittämisen, analytiikan ja testauksen parissa.
Lisäksi Volkswagenin uusia volyymisegmentin Unified cell -kennoja on määrä valmistua Salzgitterin Gigafactory-tehtaan tuotantolinjalta 2025 alkaen. Uusien Unified cell -kennojen odotetaan avaavan synergiaetuja ja vähentävän akkukustannuksia puoleen.
Vuoteen 2030 mennessä Volkswagen-konsernin tavoitteena on valmistaa akkukennoja yhdessä kumppaneidensa kanssa Euroopassa kuudella tehtaalla, joiden tuotantokapasiteetti on yhteensä 240 GWh. Salzgitterin tehtaan vuotuinen kapasiteetti tulee olemaan 40 GWh.
Aloituskuva: Audin Robin Krause ja BattMAN ReLife akkujen tarkastusjärjestelmä.